Ball valves play a crucial role in fluid control systems, utilizing a spherical element as the closure member. These valves consist of essential components, such as the valve body, seat, ball, stem, and actuators, which can be manual or powered by electric, pneumatic, or hydraulic mechanisms. The ball rotates along the valve stem’s axis, allowing precise control over the flow direction of the medium, making ball valves ideal for applications involving shutoff, distribution, or flow direction change.
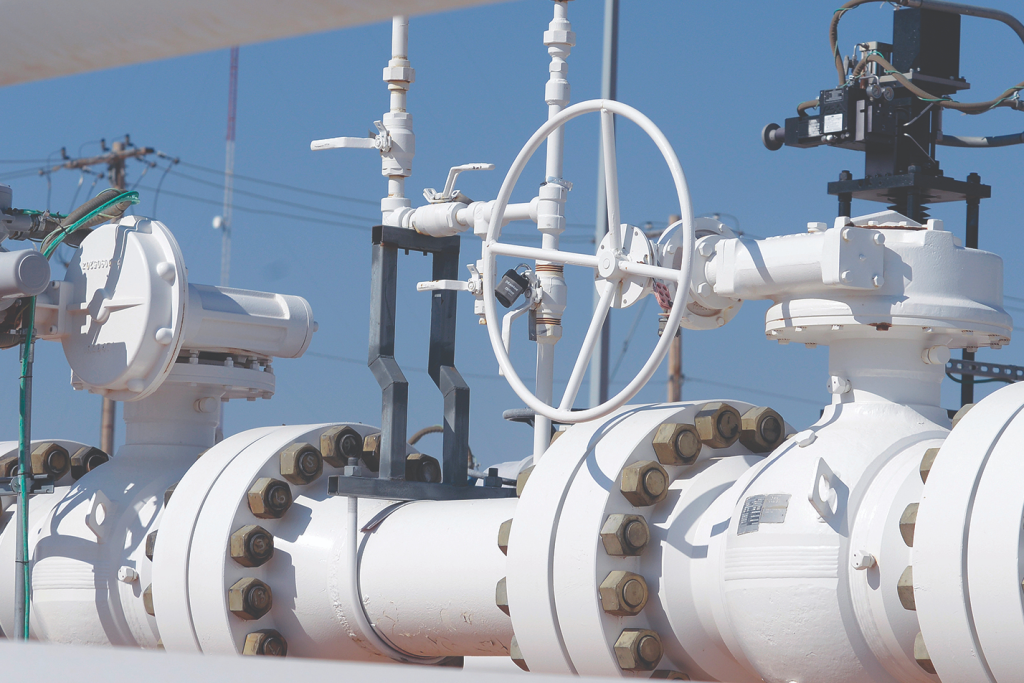
Given the variety of ball valve designs, choosing the right type depends on the operating conditions. Below, we explore the main classifications based on structural design and other factors.
Classification by Structure
1. Floating Ball Valve
In a floating ball valve, the ball is not fixed. Instead, it moves slightly under pressure, pressing against the sealing surface at the outlet to ensure a tight seal.
- Advantages: This design features simplicity and excellent sealing performance. However, the medium pressure transfers the load entirely to the sealing ring at the outlet, so the material of the sealing ring must be robust enough to withstand the pressure.
- Applications: Floating ball valves are commonly used in systems with low to medium pressure requirements.
2. Fixed Ball Valve
Unlike the floating design, the ball in a fixed ball valve remains stationary, even under pressure. Instead, the valve seats float and adjust when pressure is applied, ensuring a seal by pressing tightly against the ball.
- Advantages: Fixed ball valves are equipped with bearings on the ball’s upper and lower shafts, which reduce operating torque. This makes them ideal for high-pressure and large-diameter applications.
- Advancements: Recent innovations include oil-sealed ball valves, which inject a special lubricant between sealing surfaces, enhancing both the seal and reducing operating torque. These improvements are particularly useful in high-pressure scenarios.
3. Elastic Ball Valve
Elastic ball valves feature a ball with an elastic property. Both the ball and the seat sealing ring are made from metal, and external force is necessary to achieve an effective seal, as the medium pressure alone isn’t sufficient.
- Working Principle: The ball has an elastic groove at its lower part, which allows for expansion. When the valve closes, a wedge-shaped stem head forces the ball to expand and compress the sealing ring, ensuring a tight seal. The wedge is loosened before rotation, allowing the ball to revert to its original form, reducing friction and operating torque.
- Applications: This design is particularly suitable for high-temperature and high-pressure environments.
Other Common Classification Methods
By Flow Path Type
- Full-bore Ball Valve: The bore diameter matches that of the pipeline, offering minimal resistance and ensuring efficient flow.
- Reduced-bore Ball Valve: The bore diameter is smaller than the pipeline, making it suitable for specific applications with reduced flow requirements.
By Channel Position
- Straight-through Type
- Three-way Type
- Right-angle Type
By Temperature Rating
- High-temperature Ball Valve
- Normal-temperature Ball Valve
- Low-temperature Ball Valve
- Ultra-low-temperature Ball Valve
By Sealing Type
- Soft-seal Ball Valve: Uses non-metallic materials for sealing.
- Hard-seal Ball Valve: Ideal for high-temperature and high-pressure applications, utilizing metallic sealing materials for durability.
By Stem Mounting
- Top-mounted Ball Valve
- Side-mounted Ball Valve
By Connection Type
- Flanged Ball Valve
- Welded Ball Valve
- Threaded Ball Valve
- Clamped Ball Valve
By Drive Mechanism
- Manual Ball Valve
- Automatic Control Ball Valve: This category includes pneumatic, electric, and hydraulic types.
By Bore Size
- Ultra-large Diameter Ball Valve
- Large Diameter Ball Valve
- Medium Diameter Ball Valve
- Small Diameter Ball Valve
Ball valves are indispensable components in fluid control systems, offering a wide range of options suited to various industrial applications. By understanding the key features and applications of each type, users can make informed choices to ensure optimal system performance. Whether dealing with high pressure, large diameter, or extreme temperatures, selecting the right ball valve ensures efficiency and longevity in fluid control operations.