Magnetic drive pumps are widely used in various industrial applications due to their efficient, leak-free operation and simple design. However, to ensure optimal performance and a long service life, it is essential to follow certain precautions during their use. Below, we outline the key considerations for the safe and effective operation of magnetic drive pumps.
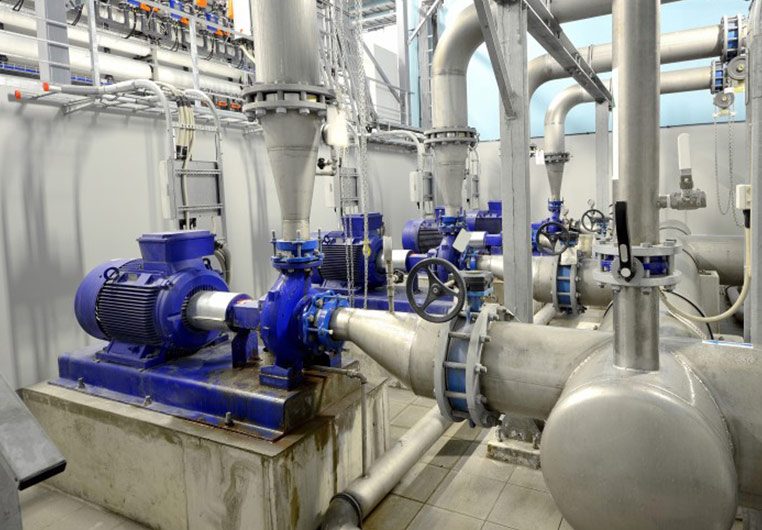
1. Avoid Dry Running
One of the most important precautions when operating a magnetic drive pump is to prevent dry running. Since the bearing cooling and lubrication rely on the medium being pumped, running the pump without liquid can damage the bearings and other internal components. Additionally, it is essential to avoid restarting the pump after a power outage while the pump is still unloaded, as this could lead to dry running, which may cause serious damage to the pump’s internal parts.
2. Use a Filter for Solid-Laden Liquids
If the medium being pumped contains solid particles, it is essential to install a filter at the pump inlet to protect the pump from damage. For liquids containing ferromagnetic particles, a magnetic filter should be used to prevent particles from damaging the magnetic coupling. This is crucial to ensure the longevity of the pump and prevent any operational issues that may arise from blockages or wear.
3. Monitor Ambient Temperature and Motor Temperature
Magnetic drive pumps should be used in environments where the ambient temperature is less than 40°C. This ensures that the pump operates within its optimal temperature range and avoids overheating. Additionally, the temperature rise of the motor should not exceed 75°C. Excessive temperatures can lead to motor failure or reduced efficiency, so regular monitoring of both ambient and motor temperatures is essential for reliable performance.
4. Check Compatibility of Medium and Temperature Range
It is essential to ensure that the medium being pumped and its temperature fall within the allowable range for the pump’s materials. For example, engineering plastic pumps should be used with liquids that have a temperature below 100°C, while metal pumps can handle similar temperature ranges but are better suited for certain high-temperature applications. The maximum suction pressure should not exceed 0.2 MPa, and the maximum operating pressure should not exceed 1.6 MPa. The density of the liquid should not exceed 1600 kg/m³, and the viscosity should not exceed 30 x 10⁻⁶ m²/s. Additionally, the liquid should not contain hard particles or fibers that could cause damage to the pump components.
5. Clean After Using Crystallizing or Precipitating Liquids
For liquids that tend to crystallize or precipitate, it is crucial to clean the pump promptly after use. Failure to do so can lead to the accumulation of deposits inside the pump, which can impair its performance and potentially cause blockages. It is recommended to flush the pump thoroughly after each use, especially when pumping viscous or precipitating liquids, to maintain its efficiency and prevent damage from solid buildup.
6. Regular Maintenance After 1000 Hours of Operation
After 1000 hours of normal operation, it is important to conduct a maintenance check on the magnetic drive pump. Specifically, the bearings and the end-face dynamic rings should be inspected for wear. Any parts that show significant wear or damage should be replaced to avoid further damage to the pump. Regular maintenance and timely replacement of worn-out parts will significantly extend the life of the pump and ensure reliable operation.
Proper operation and maintenance of magnetic drive pumps are essential to ensure their longevity and efficiency. By following the usage precautions outlined above, you can prevent common issues such as dry running, solid particle damage, and overheating, while also maintaining the pump’s reliability in demanding applications. Regular maintenance checks, especially after extended operation, will keep the pump functioning at its best and prevent unnecessary downtime or repairs. Always ensure that the pump is operating within the specified limits for temperature, pressure, and fluid characteristics to maximize performance and reliability.